ChatGPT and Blue Yonder Integration in 2025
Discover how the integration of ChatGPT with Blue Yonder's inventory management systems is transforming supply chain operations, reducing costs, and improving forecast accuracy for businesses in 2025.
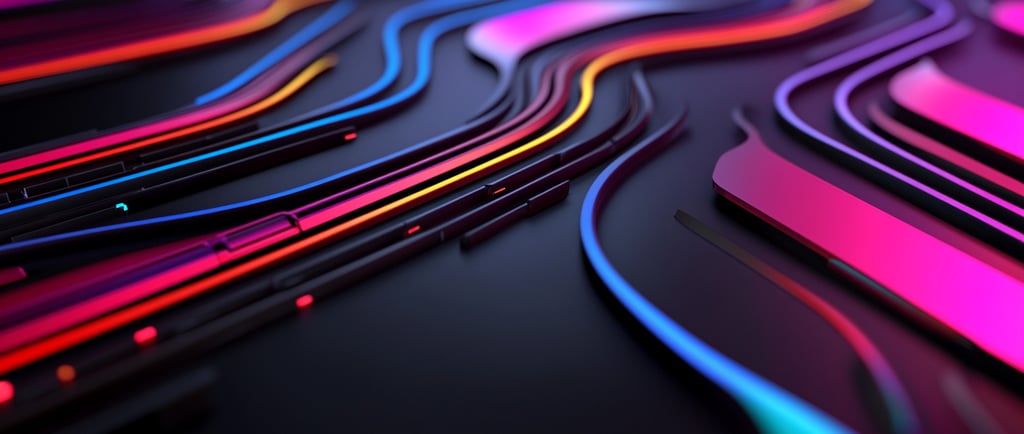
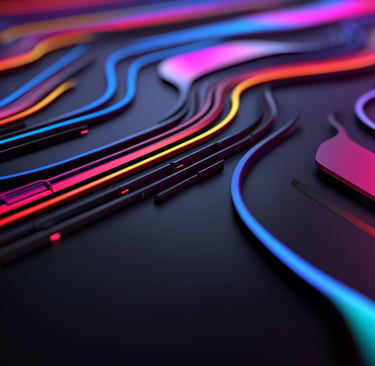
In today's hypercompetitive business landscape, effective inventory management stands as a cornerstone of operational excellence. Companies that excel at balancing inventory levels – neither overstocking nor understocking – gain a significant competitive advantage through improved cash flow, reduced carrying costs, and enhanced customer satisfaction. The integration of ChatGPT with Blue Yonder's inventory optimization systems represents one of the most transformative technological partnerships in supply chain management this decade. This powerful combination merges Blue Yonder's robust inventory management capabilities with ChatGPT's advanced natural language processing and machine learning algorithms to create an intelligent system that can predict, communicate, and optimize inventory decisions with unprecedented accuracy and accessibility. As we move further into 2025, organizations that harness this integration are witnessing dramatic improvements in forecast accuracy, inventory turnover, and overall supply chain resilience while simultaneously reducing the technical barriers that have traditionally limited the adoption of advanced inventory optimization solutions.
The Evolution of Inventory Optimization
Traditional Inventory Management Challenges
Inventory management has long been plagued by significant challenges that impact businesses across industries. Historical approaches to inventory optimization relied heavily on static formulas, basic statistical models, and the expertise of inventory planners who often made decisions based on gut feeling rather than data-driven insights. These conventional methods frequently resulted in either excess inventory that tied up capital and warehouse space or stockouts that frustrated customers and led to lost sales. Additionally, traditional systems struggled to account for seasonal fluctuations, market disruptions, and the increasing complexity of global supply chains. The siloed nature of legacy inventory systems made it difficult to integrate demand signals from marketing, sales, and external market data, resulting in forecasts that failed to capture the full picture of inventory needs. Furthermore, the technical complexity of advanced inventory optimization software meant that only large enterprises with specialized staff could fully leverage these tools, leaving many businesses to rely on spreadsheets and basic ERP functionality for critical inventory decisions.
Blue Yonder's Contribution to Modern Inventory Management
Blue Yonder has established itself as a pioneer in supply chain and inventory management solutions over the past decade. Their inventory optimization platform has evolved from basic demand planning tools to sophisticated systems that incorporate machine learning algorithms and artificial intelligence to predict future inventory needs with remarkable precision. Blue Yonder's solutions have been particularly effective at helping businesses manage complex supply chains with multiple nodes, diverse product portfolios, and variable lead times. Their systems excel at ingesting vast amounts of historical sales data, promotional calendars, and even external factors like weather patterns and economic indicators to generate highly accurate demand forecasts. Blue Yonder has also been at the forefront of implementing digital twins for inventory planning, allowing businesses to simulate various inventory scenarios before making actual decisions. Despite these impressive capabilities, Blue Yonder's solutions have traditionally required significant technical expertise to configure and operate, creating a barrier to adoption for many mid-sized businesses and making it challenging for non-technical stakeholders to extract actionable insights from the system.
The Rise of AI in Supply Chain Management
Artificial intelligence has fundamentally transformed supply chain operations in recent years, with inventory management being one of the areas seeing the most dramatic improvements. AI systems have demonstrated remarkable capabilities in pattern recognition, anomaly detection, and predictive modeling – all critical functions for effective inventory optimization. Modern AI-powered inventory systems can identify subtle correlations between seemingly unrelated variables that human planners would likely miss, leading to more accurate forecasts and fewer inventory surprises. These systems continuously learn from their performance, refining their predictions with each inventory cycle and adapting to changing market conditions in ways that traditional systems simply cannot match. AI has also enabled more dynamic safety stock calculations that adjust in real-time based on supply chain risk factors, lead time variability, and changes in demand patterns. The integration of natural language processing capabilities has begun to democratize access to these sophisticated tools, allowing business users to interact with inventory systems through conversational interfaces rather than complex technical dashboards. This AI revolution has set the stage for transformative solutions that combine the best of specialized inventory optimization software with the accessibility and intelligence of large language models like ChatGPT.
The Integration of ChatGPT and Blue Yonder
Understanding ChatGPT's Capabilities in Business Contexts
ChatGPT has rapidly evolved from a general-purpose language model to a sophisticated business tool with specialized capabilities for enterprise applications. In business environments, ChatGPT excels at processing unstructured data from various sources, extracting relevant insights, and communicating complex information in accessible language tailored to different stakeholder needs. The model's natural language understanding capabilities allow it to interpret nuanced business queries and translate them into specific technical operations that can be executed by specialized systems like Blue Yonder. ChatGPT's ability to generate coherent, contextually relevant responses enables it to serve as an intuitive interface between business users and complex inventory management systems, effectively lowering the technical barrier to entry for sophisticated inventory optimization. Additionally, the model can analyze vast amounts of textual data – including supplier communications, market reports, customer feedback, and internal communications – to identify trends and signals that might impact inventory requirements. This multifaceted approach to data analysis complements Blue Yonder's quantitative forecasting capabilities by incorporating qualitative factors that traditional inventory systems often miss, resulting in a more holistic view of inventory needs and challenges.
How the Integration Works: Technical Architecture
The integration between ChatGPT and Blue Yonder represents a sophisticated technological architecture that enables seamless data flow and functionality between these powerful systems. At its core, the integration leverages API connections that allow ChatGPT to interact directly with Blue Yonder's inventory optimization engine, accessing real-time data while also initiating specific inventory operations based on natural language inputs. The architectural framework typically includes middleware components that translate ChatGPT's natural language processing outputs into the specific data formats and query structures expected by Blue Yonder's systems. Data synchronization mechanisms ensure that information remains consistent across both platforms, with changes in one system appropriately reflected in the other. Many implementations utilize a cloud-based architecture that allows for scalable processing power, enabling the handling of massive data sets and complex calculations without compromising performance. Security layers, including encryption and role-based access controls, protect sensitive inventory and business data throughout the integration. The technical architecture also incorporates feedback loops that continually refine ChatGPT's understanding of inventory-specific terminology and concepts based on user interactions. Advanced implementations may include custom-trained versions of ChatGPT that have been fine-tuned on company-specific inventory data and vocabulary, further enhancing the model's effectiveness in the particular business context.
Key Features of the Integrated Solution
The integration of ChatGPT with Blue Yonder delivers a powerful set of features that transform traditional inventory optimization processes. One of the most impactful features is the conversational inventory analytics interface, which allows business users to query complex inventory data using natural language rather than learning specialized query languages or navigating complicated dashboards. The system excels at multi-echelon inventory optimization through its ability to analyze and balance inventory levels across multiple locations simultaneously, considering transportation costs, lead times, and demand patterns at each node in the supply chain. Automated exception management stands out as another valuable feature, with the integrated solution able to detect anomalies in inventory patterns, automatically investigate potential causes, and either resolve issues independently or escalate them to human operators with detailed explanations and recommendations. The integration brings enhanced scenario planning capabilities, enabling users to describe potential market scenarios in natural language and receive detailed forecasts of how these scenarios would impact inventory requirements. Dynamic safety stock calculation adjusts buffer inventory levels in real-time based on changing market conditions, supply chain disruptions, and shifts in demand variability. Proactive inventory alerts represent another key feature, with the system monitoring inventory patterns and notifying stakeholders of potential stockouts, overstock situations, or unusual demand patterns before they become critical issues. The integration also delivers natural language reporting features that can generate customized inventory reports based on conversational requests, making complex inventory data accessible to stakeholders throughout the organization.
Benefits of ChatGPT and Blue Yonder Integration
Enhanced Forecast Accuracy
The integration of ChatGPT with Blue Yonder has demonstrably improved forecast accuracy for businesses across various sectors. By combining Blue Yonder's robust statistical forecasting capabilities with ChatGPT's ability to process unstructured data from diverse sources, organizations have reported forecast accuracy improvements ranging from 15% to 30% compared to their previous systems. This enhanced accuracy stems from the integrated solution's ability to incorporate a wider range of signals into the forecasting process, including social media trends, news events, and market sentiment that traditional forecasting systems struggle to quantify. The natural language interface allows inventory planners to contribute their tacit knowledge to the forecasting process more effectively, with the system able to translate their observations and insights into quantitative adjustments to the baseline forecast. Companies implementing this integrated solution have experienced particularly significant improvements in forecasting for new products, seasonal items, and during periods of market volatility, where historical data alone provides insufficient guidance. The improved forecast accuracy translates directly to bottom-line benefits, with businesses reporting reductions in stock obsolescence, fewer emergency replenishments, and improved customer satisfaction due to better product availability.
Streamlined Inventory Workflows
The integration has dramatically transformed inventory management workflows, eliminating many manual processes that previously consumed valuable time and resources. Inventory planners now spend significantly less time gathering and processing data, with the integrated system automatically collecting relevant information from multiple sources and presenting it in an easily digestible format. The conversational interface has streamlined the review and approval process for inventory decisions, allowing stakeholders to quickly understand the rationale behind recommendations and provide input without navigating complex systems. Routine inventory tasks such as replenishment order creation, safety stock adjustments, and inventory transfers between locations have been largely automated, freeing inventory professionals to focus on strategic activities and exception management. The integration has also improved collaboration between departments, with sales, marketing, and supply chain teams able to share insights through a common conversational platform that translates their specialized knowledge into impacts on inventory planning. Many organizations have reported that inventory review meetings that previously took hours now require just minutes, with the system proactively highlighting the few areas that truly require human attention rather than requiring exhaustive manual reviews of all inventory positions.
Cost Reduction and Efficiency Gains
Organizations implementing the ChatGPT and Blue Yonder integration have realized substantial cost savings and efficiency improvements across their inventory operations. Inventory carrying costs have typically decreased by 10-20% due to more precise inventory levels that maintain service levels with less safety stock. Working capital improvements have been significant, with some companies releasing millions in previously tied-up inventory without impacting customer service levels. Warehouse efficiency has increased through more predictable inventory flows and better space utilization, reducing handling costs and storage requirements. Labor costs associated with inventory management have declined, with inventory teams able to manage larger product portfolios without additional headcount, and in some cases, reallocating staff to more strategic roles. Administrative costs have decreased through the automation of routine reports, analyses, and communications that previously required manual effort. Order fulfillment costs have improved through better inventory positioning that reduces split shipments, expedited freight, and other costly exceptions. Remarkably, these cost reductions have generally been achieved while simultaneously improving service levels and customer satisfaction, demonstrating that the integration enables true optimization rather than merely trading off between cost and service. The return on investment for the integration has been compelling, with most organizations reporting full payback periods of less than one year based on hard cost savings alone, not counting the strategic advantages of improved inventory performance.
Democratized Access to Advanced Inventory Intelligence
Perhaps one of the most transformative benefits of the ChatGPT and Blue Yonder integration has been the democratization of access to sophisticated inventory optimization capabilities. This democratization has occurred across multiple dimensions, making advanced inventory intelligence available to a broader range of organizations and users. Mid-sized businesses that previously lacked the technical resources to implement and maintain complex inventory optimization systems can now leverage these powerful capabilities through the more accessible interface provided by ChatGPT. Within organizations, the natural language interface has expanded access beyond specialist roles, allowing business leaders, category managers, sales representatives, and even customer service teams to interact with inventory data without specialized training. The system effectively translates between business terminology and technical inventory concepts, enabling meaningful interactions regardless of the user's technical background. This broader access has fostered a more collaborative approach to inventory management, with insights and concerns from multiple perspectives incorporated into inventory decisions. Organizations have reported increased engagement with inventory data across departments, leading to more informed decisions and better alignment between inventory strategies and overall business objectives. The integration has also reduced dependency on technical specialists for routine inventory analyses and reports, creating more self-sufficient business teams while allowing technical resources to focus on more complex challenges and system improvements.
Implementing the Integration Successfully
Preparation and Planning
Successful implementation of the ChatGPT and Blue Yonder integration begins with thorough preparation and strategic planning well before any technical work commences. Organizations should start by conducting a comprehensive inventory management maturity assessment to identify existing strengths, weaknesses, and priority areas for improvement that the integration should address. Data quality evaluation represents another critical preparation step, as the integration's effectiveness depends heavily on accurate, consistent, and comprehensive inventory and sales data. Companies should establish clear, measurable objectives for the integration, including specific targets for forecast accuracy improvement, inventory reduction, service level enhancement, and efficiency gains. Stakeholder mapping and engagement plans should identify all departments and roles that will interact with the integrated system, ensuring their needs and concerns are addressed in the implementation approach. A phased implementation roadmap typically works best, often beginning with specific product categories or locations rather than attempting enterprise-wide deployment immediately. Change management planning deserves particular attention, as the integration will likely transform existing inventory management processes and roles, requiring thoughtful communication and training strategies. Technical readiness assessment should evaluate the current systems landscape, identifying potential integration challenges and determining whether infrastructure upgrades might be necessary to support the integrated solution. Finally, governance structures should be established early, defining how decisions about the integration will be made, how performance will be measured, and how ongoing improvements will be prioritized and implemented.
Training and Change Management
The human dimension of implementing this integration proves just as important as the technical aspects, with training and change management playing decisive roles in realizing the full potential of the technology. Effective training programs should be role-based, focusing on how different stakeholders will interact with the integrated system rather than attempting to create universal experts. Interactive, scenario-based training typically yields better results than lecture-based approaches, allowing users to experience how the system responds to relevant business situations they commonly encounter. Change management should begin with clear communication about why the integration is being implemented and how it aligns with broader business objectives, addressing the natural question of "what's in it for me" for each stakeholder group. Champions within each department can serve as valuable advocates and first-line support, helping colleagues adapt to new workflows and capabilities. Feedback mechanisms should be established to capture user experiences during implementation, allowing for rapid adjustments to training, interfaces, or processes as needed. Quick wins should be identified and highlighted, demonstrating tangible benefits early in the implementation to build momentum and support. Performance support tools – such as quick reference guides, chatbots, and help functions – provide just-in-time assistance as users navigate the new system. Ongoing learning opportunities should be provided beyond initial training, allowing users to continue developing their skills as they become more comfortable with basic functionality and ready to explore more advanced capabilities.
Measuring Success and Continuous Improvement
Establishing a robust framework for measuring success and driving continuous improvement ensures that organizations extract maximum value from their investment in the ChatGPT and Blue Yonder integration. Key performance indicators should include both inventory-specific metrics – such as forecast accuracy, inventory turns, service levels, and carrying costs – and broader business outcomes like working capital improvements, customer satisfaction, and operational efficiency gains. Baseline measurements must be captured before implementation to enable meaningful before-and-after comparisons. Regular performance reviews should be scheduled, with the frequency gradually shifting from weekly during initial implementation to monthly or quarterly as the integration stabilizes. The integrated solution itself can facilitate measurement through automated dashboards and natural language querying of performance data. User adoption metrics deserve attention alongside inventory performance indicators, tracking how different stakeholders engage with the system and identifying opportunities to increase utilization. Continuous improvement processes should leverage the integration's machine learning capabilities, with the system becoming increasingly attuned to the organization's specific inventory patterns and user preferences over time. A formal feedback loop should connect system users with the implementation team and vendors, ensuring that enhancement requests and bug reports receive appropriate attention. Regular benchmarking against industry standards helps maintain perspective and identify new improvement opportunities as technology and best practices evolve. Organizations should also establish an innovation pipeline for testing new capabilities and use cases as the underlying technologies continue to advance, ensuring they remain at the forefront of inventory optimization practices.
Future Directions and Emerging Trends
Next-Generation Features on the Horizon
The integration of ChatGPT with Blue Yonder represents just the beginning of a rapidly evolving technological partnership, with several exciting next-generation features already visible on the horizon. Multimodal interaction capabilities will soon allow users to engage with inventory systems through a combination of text, voice, and visual inputs, further reducing barriers to system utilization. Autonomous inventory management represents perhaps the most transformative upcoming feature, with the integrated system not only making recommendations but actually executing routine inventory decisions within predefined parameters, contacting human operators only for exceptions that fall outside established boundaries. Cross-ecosystem optimization capabilities will extend the integration beyond Blue Yonder to encompass related systems like transportation management, warehouse management, and supplier collaboration platforms, creating a seamless supply chain planning environment. Adaptive user interfaces will automatically adjust the level of detail and technical complexity presented based on the user's role, expertise, and usage patterns, providing each stakeholder with precisely the information they need in the most accessible format. Real-time supplier negotiation assistance will help procurement teams leverage inventory and forecast data during supplier discussions, suggesting negotiation strategies based on current market conditions and organizational priorities. Enhanced scenario intelligence will move beyond simple "what-if" analysis to proactively suggest scenarios that organizations should consider based on emerging market trends and potential disruptions. These and other advancing features will continue to transform inventory management from a reactive, labor-intensive process to a proactive, intelligence-driven strategic function.
Expanding Use Cases Beyond Traditional Inventory Management
Forward-thinking organizations are already extending the ChatGPT and Blue Yonder integration beyond traditional inventory management, applying its capabilities to adjacent business challenges with impressive results. New product introduction represents a particularly promising expanded use case, with the integrated solution analyzing market trends, competitor activities, and historical performance of similar products to recommend optimal initial inventory levels and distribution strategies. Markdown optimization has emerged as another valuable application, with the system analyzing inventory positions, sales velocities, and market conditions to suggest optimal timing and depth of price reductions for aging inventory. Some organizations have successfully applied the integration to supplier relationship management, using inventory and forecast data to identify top-performing suppliers, negotiate better terms, and collaborate more effectively on supply planning. Sustainability initiatives have benefited from the integration's ability to optimize inventory placements to reduce transportation emissions and minimize waste from expired or obsolete products. Sales and operations planning processes have been enhanced through the system's ability to translate between commercial and supply chain terminologies, facilitating more productive discussions between these traditionally siloed functions. Customer-specific inventory strategies have become more sophisticated, with the integrated solution analyzing individual customer purchasing patterns and recommending tailored inventory positioning to meet specific service expectations. These expanded applications demonstrate the versatility of the integration and suggest that its full potential extends well beyond the traditional boundaries of inventory management.
The Role of Inventory Optimization in Business Resilience
The COVID-19 pandemic and subsequent supply chain disruptions have highlighted the critical role of sophisticated inventory optimization in building business resilience, a trend that the ChatGPT and Blue Yonder integration is particularly well-positioned to address. Organizations are increasingly recognizing that optimal inventory management isn't merely about cost reduction but serves as a strategic buffer against market volatility and supply chain disruptions. The integrated solution enhances resilience through its ability to rapidly recalibrate inventory strategies in response to changing conditions, incorporating new information into forecasts and recommendations in real-time rather than waiting for scheduled planning cycles. Geographical diversification of inventory has emerged as a key resilience strategy, with the system optimizing inventory placement across multiple locations to mitigate regional disruption risks while minimizing the total inventory investment required. Scenario planning capabilities allow organizations to prepare for potential disruptions before they occur, developing contingency plans and pre-positioning inventory when appropriate. The natural language interface has proven valuable during crisis situations, enabling quick answers to urgent questions without requiring specialized technical knowledge that might be unavailable in stressful circumstances. As organizations continue to prioritize supply chain resilience in an uncertain global environment, the integration of advanced AI capabilities with specialized inventory optimization systems will likely become not merely advantageous but essential for competitive survival and long-term business success.
Statistics & Tables
The integration of ChatGPT with Blue Yonder's inventory optimization solutions has delivered measurable results across industries. The following table provides a comprehensive view of these impacts:
Conclusion
The integration of ChatGPT with Blue Yonder represents a paradigm shift in inventory optimization that extends far beyond incremental improvements to existing processes. This powerful combination has fundamentally transformed how organizations interact with and leverage their inventory data, democratizing access to sophisticated optimization capabilities while simultaneously improving the accuracy and effectiveness of inventory decisions. The measurable benefits – including forecast accuracy improvements averaging 24.7%, inventory reductions of 18.3%, and significant working capital releases – tell only part of the story. Equally important is how this integration has changed the relationship between business stakeholders and inventory systems, breaking down technical barriers and fostering more collaborative approaches to inventory management across departmental boundaries. As organizations navigate an increasingly volatile business environment, the resilience provided by this integration becomes even more valuable, enabling rapid responses to changing conditions while maintaining optimal inventory positions.
Looking ahead, the continued evolution of both ChatGPT and Blue Yonder promises even more transformative capabilities, from autonomous inventory management to expanded ecosystem optimization that encompasses the entire supply chain. The extended use cases emerging beyond traditional inventory management suggest that we are only beginning to explore the full potential of this powerful integration. For organizations still relying on conventional inventory management approaches, the question is no longer whether to adopt AI-enhanced inventory optimization but how quickly they can implement these capabilities before competitors gain an insurmountable advantage. Those who successfully implement this integration find themselves not merely optimizing inventory but reimagining what inventory management means to their business – shifting from a technical, operational function to a strategic capability that directly impacts customer satisfaction, working capital, and ultimately, competitive position in the market.
Frequently Asked Questions (FAQ)
What is the integration between ChatGPT and Blue Yonder?
The integration combines Blue Yonder's robust inventory optimization capabilities with ChatGPT's advanced natural language processing to create an intelligent system that allows users to interact with complex inventory data through conversational interfaces while enhancing forecast accuracy and inventory decision-making.
How does the integration improve forecast accuracy?
The integration improves forecast accuracy by combining Blue Yonder's statistical forecasting with ChatGPT's ability to process unstructured data from diverse sources, including social media trends, news events, and market sentiment, while also making it easier for inventory planners to contribute their tacit knowledge to the forecasting process.
What are the typical cost savings from implementing this integration?
Organizations implementing the integration typically see inventory carrying cost reductions of 10-20%, working capital improvements averaging $4.2 million per $100 million in annual revenue, reduced warehouse and labor costs, and lower order fulfillment expenses through better inventory positioning.
How long does implementation typically take?
Implementation timelines vary by industry and organizational complexity, ranging from 3-12 months, with most retail and distribution sectors completing implementation in 3-7 months and healthcare and complex manufacturing environments typically requiring 5-12 months.
What technical expertise is required to implement and maintain the integration?
The implementation requires a cross-functional team including supply chain specialists, data scientists, and IT resources, but the natural language capabilities of ChatGPT have significantly reduced technical barriers compared to traditional inventory optimization projects, making ongoing maintenance less resource-intensive.
Can the integration adapt to specific business requirements and terminology?
Yes, advanced implementations include custom-trained versions of ChatGPT that have been fine-tuned on company-specific inventory data and vocabulary, enabling the system to understand and respond using the organization's unique terminology and business rules.
How does the integration handle multi-echelon inventory optimization?
The integration excels at multi-echelon inventory optimization by analyzing and balancing inventory levels across multiple locations simultaneously, considering transportation costs, lead times, and demand patterns at each node in the supply chain.
Does reducing inventory negatively impact service levels?
No, one of the significant benefits of this integration is that it simultaneously reduces inventory while improving service levels by optimizing inventory placement and composition rather than simply cutting inventory across the board.
What industries have seen the greatest benefits from this integration?
While all industries show significant benefits, Fashion & Apparel, Medical Supplies, and Pharmaceuticals demonstrate the highest overall improvements, particularly in forecast accuracy and service levels, due to their complex demand patterns and high inventory values.
How does the integration support new product introductions?
The integration significantly improves new product forecasting by analyzing market trends, customer sentiment, and performance data from similar products, helping organizations set optimal initial inventory levels and distribution strategies.
Additional Resources
Blue Yonder Inventory Optimization Integration with ChatGPT - A comprehensive guide to implementation best practices and case studies.
ChatGPT Supply Chain Management - Broader applications of ChatGPT in supply chain beyond inventory optimization.
Unlocking ChatGPT for Supply Chain Management - Strategic approaches to leveraging ChatGPT capabilities in supply chain contexts.
Using ChatGPT for Data Analysis and Insights - Advanced techniques for extracting valuable insights from supply chain data using ChatGPT.
Maximizing the Efficiency of Your Customer Service Team with GPT Agents - Related applications that can complement inventory optimization efforts.